Expect the unexpected: 3 ways to manage fulfilment spikes
Today’s supply chain is ever-evolving. Changing consumer desires can make anticipating demand spikes seem like finding a needle in a haystack. According to a Barclays study, 67 percent of UK warehouse managers find coping with peak periods a significant challenge, while 1 in 2 feel the same about demand forecasting.
As a result, the superior customer experience consumers have come to expect can often suffer. But there are strategies to help your warehouse profit from demand spikes rather than suffer because of them. Consider these three ways to re-evaluate your warehouse and manage both expected holiday peak seasons and other surprise peak seasons throughout the year.
The right staff gets the job done
Traditional peak season demand continues to grow exponentially. A recent Ingenico Group study found that U.K. consumers spent 515 percent more online on Black Friday in 2017 than any average Friday during the year. And though automation is gaining a foothold in the warehouse, technology can’t handle this uptick in demand alone – seasonal workers are here to stay.
Still, warehouses often struggle to find the balance between under and overtraining seasonal pickers and packers. Undertraining can be a peak season money pit, leading to a lack of preparedness and efficiency that echoes throughout your warehouse processes. Overtraining isn’t profitable either, as you’ll expend unnecessary time and resources.
Before peak seasons hit, re-evaluate your onboarding processes. Try to assign temporary employees to simpler tasks to reduce training time, and leave the more complex tasks to your seasoned staff. This can help you avoid critical mistakes in processes because of unqualified workers managing your most challenging operations. Standardizing your training process can also help you avoid wasting valuable time for your year-round staff in orientation activities.
Your relationship with seasonal staff shouldn’t end after the holidays. Keeping track of employees’ availability throughout the year, along with their skills in the warehouse, can help you maintain a comprehensive database of staff to utilize during unexpected peaks, without time wasted on training new employees.
Organize for success
The picking process can often sap your team’s productivity. More efficient picking lets you ship more items per hour and subsequently increases profitability. To ensure your warehouse resources are being used efficiently, make sure your team can maneuver through aisles in the most logical way.
A warehouse management system (WMS) allows you to track purchase trends over time, helping you better prepare for unexpected inventory changes. Trend analyses allow you to use data to predict which items will be in high demand at varying times of the year and enable you to reorganize your warehouse in preparation. It can also allow you to relocate items that often sell together, saving your workers from searching the entire warehouse to fulfil a single order.
Though you can’t predict every demand spike, you can streamline your picking processes to develop a mindset of efficiency throughout your entire warehouse – and quickly adapt to sudden changes in demand as they come into play.
Flexible technology is key
A warehouse can’t reach peak efficiency without a complete understanding of the data surrounding its processes. A best-of-breed WMS provides deeper visibility into these processes and data points – but user restrictions can often burden your operations and scalability.
Flexible licensing is a valuable feature in warehouse management technology. It allows for higher numbers of employees to have access to software during demand spikes. Managers can even temporarily turn some tasks over to their assistants to ensure every part of the warehouse operates like a well-oiled machine.
Flexible licensing, combined with extensive functionalities, allow a WMS to help your warehouse grow without a significant upfront investment. The right WMS will help you and your operations grow today and will scale alongside your operations as you expand in the future.
Your “peak season” is unique. Your technology should be too.
Today’s “now” economy fuels a more capricious supply chain. Consumers demand more options, quicker delivery, and an overall seamless shopping experience – without consideration to the back-end processes. Unexpected peak seasons can exacerbate these fulfilment challenges.
Still, avoid letting demand spikes hinder your warehouse processes. With the proper evaluation and a best-of-breed warehouse management system, you can harness peak season opportunities to deliver a superior customer experience and empower greater efficiency throughout your warehouse.
Free white paper
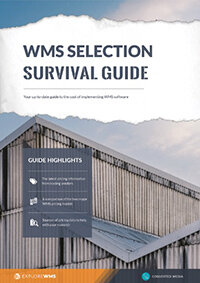
WMS selection survival guide
Exclusive, six-step guide to finding the best WMS for your business
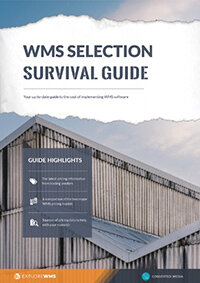
Related articles
-
What functionality manufacturing companies need from WMS
The top features manufacturers should look for when selecting WMS
-
Mission-critical features of food lot traceability software
What features of food traceability software will help you during a food recall
-
3 reasons WMS is crucial for mastering multichannel fulfillment
Exclusive guest blog from Snapfulfil discussing multichannel fulfillment and WMS