Improving warehouse efficiency with WMS
Every WMS discussion comes back to improving warehouse efficiency. That’s the software’s biggest claim to fame and the greatest potential. It’s where most will find their savings or even discover an ability to expand and better serve customers.
There are many different ways to achieve WMS efficiency gains, and we’ve decided to look at three that are present in nearly every WMS implementation.
Improve inventory management
A WMS provides many tools around inventory location and usage in your warehouse or multiple locations. Automated cycle counts and continuous updates based on real-time picking information can help you avoid running out of stock and having to pause or cancel orders.
Your team will also have better data for restocking, basing the resupply level on comparisons of current orders as well as historical data. If July and August are a significant time for your business but this Spring was busier than average as well, combining the two datasets can help you decide if it’s right to order more for this Summer.
Plan your floor
Improving warehouse efficiency starts with the layout of the floor. Knowing the best way to organize a warehouse can be challenging, but many modern WMS include layout and design tools to help. The most useful aspect of this is their ability to collect data on individuals and teams, seeing where people go the most and identifying bottlenecks.
Warehouse layout should specifically address three core concepts:
- Every product location is easily accessible by the relevant person or equipment. You don’t want to have to move one product to get to another, and there needs to be enough room for equipment like pallet jacks to maneuver if they’re required.
- There’s enough space, but not too much. Maximizing your space allocation involves all the inventory management mentioned first as well as your storage requirements for pallets and other goods, office space, workspace areas, freestanding equipment, and anything specific to your operations.
- Workflow. Everything is finalized with a proper understanding of how your people pick, areas of congestion, and what you need to avoid bottlenecks.
WMS efficiencies often come by reducing traffic, eliminating how much your team has to walk, and even adapting picking and load processes based on space so you can get more done, faster.
Eliminate paperwork tasks
One of my favorite things about a WMS is that it lets warehouse crews focus on products and tasks instead of data entry. Voice-picking and handheld scanners keep paper off your floor (which is incredibly easy to misplace). Electronic signature capture ensures no one has to bring forms up to the office and the smartest systems can even immediately flag issues in what you’re receiving.
Accurate pick lists also make it easier for your team to use wave and batch picking to fill orders faster, as workers scan items instead of needing to maintain physical checklists.
In short, less paperwork means fewer errors.
Adopt what’s next
The final element to note is that WMS efficiency gains don’t stop after implementation. A robust system is part of a long-term warehouse improvement plan that allows you to enjoy future innovation. WMS using standardized databases are simpler to integrate with new voice picking technology as well as some drones that are starting to perform inventory counts.
Free white paper

WMS requirements template
Over 120 WMS feature ideas to help you build a requirements list and shortlist vendors
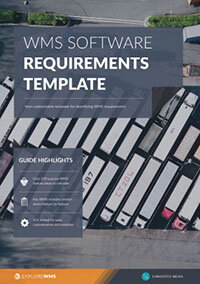
Related articles
-
What are the biggest WMS challenges in warehouse management?
The top problems warehouses face and how WMS helps them
-
Mission-critical features of food lot traceability software
What features of food traceability software will help you during a food recall
-
The benefits of a warehouse inventory system
The benefits WMS provides inventory management in the warehouse