Areas with the highest ROI for WMS
Warehouse management ROI can feel extremely daunting because it’s such a broad topic, and the total value is difficult to grasp.
If you look purely at fulfillment metrics, are you missing ROI value around internal efficiencies? Does error reduction properly cover employee satisfaction? Can prioritizing a lean supply chain cost more if you’re not considering recurring shipping and lifetime storage costs?
Complexity comes rushing up to meet our feet as soon as those big questions get raised. So, let’s start a little differently and look at specific ROI impact areas in the warehouse. The places where you can see early gains and determine if a process is worth it.
Based on conversations with WMS vendors and warehouse operators, there are three large areas of warehouse cost that have clear WMS benefits. You might just find that the gains you make here already get you to positive ROI territory, allowing every other gain to be icing on the cake.
Labor utilization and management
On average, your labor will cost between 60% and 65% of your warehouse budget. One of the functions of a warehouse management system is to set schedules and monitor metrics around your staff. This can show you who is most efficient at which task, who needs help, which products require more human action, and how to scale your workforce.
Workforce optimization modules are available from many leading WMS providers, and they’ve become a major focus in WMS marketing because of their importance to client success and ROI.
You can also improve ROI thanks to a WMS that simplifies labor-intensive activities. Options include updating or consolidating picking lanes, using advanced picking techniques to redistribute actions, and even changing staff levels for different shifts when you expect gains in inbound, outbound, and more.
Error reduction
Fulfillment errors cost a business roughly $35 to $50 per error in direct costs, even picking errors of 1% or 2% can translate into hundreds of thousands of dollars lost each year. Total losses climb even higher if a fulfillment error is grave enough to cost you a major client or partner. For companies who rely on Amazon and other eCommerce services for part of their sales, error rates decrease customer satisfaction rates, putting you in danger of losing these major sales channels.
Software in your warehouse is one of the safest routes you can take to address this concern because the top benefits of a WMS come in the realm of process accuracy and speed improvements, which research says are “the two most dominant performance objectives to achieve” to reduce human error.
A WMS removes many manual processes, incorporates a variety of scans and checks during the fulfillment process, and can help your team work smart with zone or batch picking, instead of having a single staff member run across your entire warehouse for each order.
Give people a helping hand with a system that verifies the accuracy of their work as it happens, and provides prompts when a change is needed, instead of a more manual process that discovers errors only when an order is returned.
Forecasts and planning
How much inventory is sitting on your shelves for more than 3 or 6 months? On the other hand, how many orders are delayed or lost because of out-of-stocks?
In the retail world, where data is a little more available, we see that there’s at least $22 billion worth of sales that get lost or captured by competing brands and products due to out-of-stocks. In the U.S., for example, 15% delay or cancel orders when inventory isn’t there, and at least another 30% change brands.
Not having the right goods is worse than leaving money on the table because these buyers are also establishing relationships with your competitors.
Where does WMS return on investment come into play here? Demand planning and forecasting. Understanding your inventory with a smart tracking system can help you understand orders, adapt to dramatic changes, and even automate notices to partners that you’ll need a bigger order than usual next time.
Today, WMS analytical tools come standard in most cases. Use these to look at as much data you have from the past. Create your baselines and seek out trends. Planning for what will happen tomorrow and in two months can ensure you’ve got the right goods and materials, while also getting rid of the rest.
Once you learn the basics, the ROI for WMS analytics can continue to increase. You can look at those lucrative, but slow-selling products and understand the best inventory levels and resupply orders to minimize shipping and storage costs, while avoiding out-of-stocks that cost big money.
Free white paper
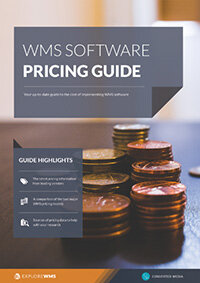
WMS software pricing guide
Your up-to-date guide to the cost of WMS software
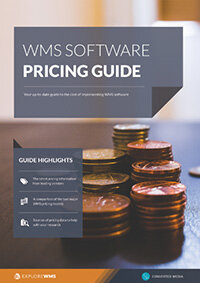
Related articles
-
What are the biggest WMS challenges in warehouse management?
The top problems warehouses face and how WMS helps them
-
Mission-critical features of food lot traceability software
What features of food traceability software will help you during a food recall
-
The benefits of a warehouse inventory system
The benefits WMS provides inventory management in the warehouse